Applications - All > Applications - Selecting Products
How to choose thermal insulation/protection tape for hose, tube, pipe, wire and cable protection


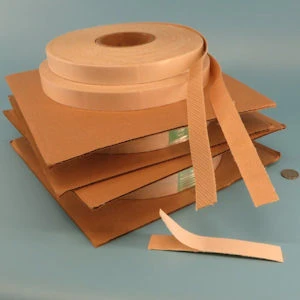
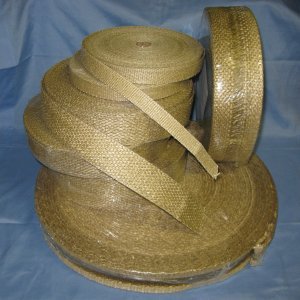
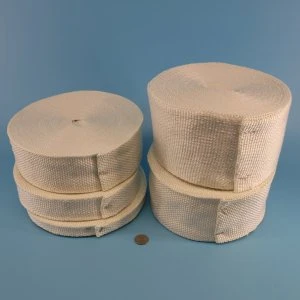
How to select insulation tape for hose, tube, pipe, wire and cable thermal protection
Keeping heat in or out
Both sleeves and tapes can be used to protect hoses, tubing, pipe, wire and cables. Tapes may be easier to install in situ as a sleeve requires disconnecting one end for installation. Tapes may require additional mounting techniques to keep them in place compared to the ease in which a sleeve is installed.
When a thermal protection tape is added to a hose (or tube/pipe/wire/cable), it adds a thermal time delay to the heat transfer between the hose and the environment it is installed in.
Tapes are generally wound in a spiral fashon along the length of the hose/tube/pipe/wire/cable, and commonly overlapped by 50%. In this fashion, a tape provides two layers of insulation thickness per wrap. Knitted tapes generally are more conformable than woven tapes when wrapping anything with curves, bends or elbows.
Generally a full wrap is made at the starting location, and a full wrap at the end location. The start and end locations can be secured with metal clamps or tie wraps, or with lock wire. Additinal clamps, tie wraps or lock wire should be used at intervals along the wrap.
How many layers of tape to use will depend on the goals of the application and the thermal insulation value required. Different types of tapes can be layered if necessary - such as an insulating layer to start and a protection layer over top to finish.
If the assembly (the hose/tube/pipe with the protection sleeve) is carrying a hot fluid, then the insulation tape helps to keep the assembly from cooling, and the surface temperature of the insulation tape will be lower than the surface of the inner hose. This is particularly useful in situations where we are trying to keep hot process fluids from cooling, and also useful in providing burn protection to personnel who may come into casual contact with the assembly if the temperature of the assembly is above the normally accepted 203F safety limit for non-metallic objects.
Generally, the thicker the insulation layer, then the more heat that is kept inside the assembly and the lower the surface temperature of the outside of the insulation will be. That thickness is usually practically effective up to 2" of insulation thickness. After that, adding thickness does not provide much of a benefit but adds cost.
The reverse is also true. If the environment is hot, then the insulation helps to prevent the assembly inside from heating. For example a chiller line or liquid nitrogen/oxygen line. Another example would be instrumentation or robotic welding inside an operational oven or furnace.
Flow in a hose/pipe can provide cooling/heating
Now take into account a situation where a liquid or gas medium is flowing in the hose, and the hose is passing through a hotter environment. As the medium passes through the hose it absorbs heat from the warmer insulation layer. If the flow is very slow, then the heat gain is more than if the flow is faster. So a faster flowing medium in the hose would remain cooler by reducing the heat gain as it flows inside the hot environment area for a shorter time.
If there is very low flow (or none in the case of wires and cables) then the hose inside the assembly will eventually reach the same temperature as the environment, but it will take time to do so. In cases where the temperature of the hot environment cycles, for example from room temperature to 1000F and then back to room temperature, then the insulation layer only needs to be thick enough to add a time delay greater than the cycle time in order to keep the assembly cooler. If the temperature cycle time is short, just a few seconds or perhaps a few minutes, then a thin insulation layer may work. If the cycle length is long, perhaps hours or days, then eventually the heat will permeate the insulation layer and be transferred into the hose (or wires, cables).
Cycle time is an important consideration
In such a situation even the thickest of insulation tapes may not be enough to keep the protected assembly from reaching a point where it exceeds its material design temperature. As an example, an insulation blanket for a generator exhaust pipe would have a design internal temperature of 1000F, and with a 1" insulation layer the outside fabric of the blanket will reach just over 200F in a room temperature environment. If the same insulation blanket were made to keep the inside assembly cool and the external environment was at 1000F, then the internal temperature of 200F or higher would be over the limit, for example, of hoses or wiring that was rated to 200F. In this case the solution may be to use a 2" thick insulation instead of 1" thick. Again, however, the assembly inside may still reach the same temperature as the outside environment - it will just take longer to do so.
So the choice of material of the insulation tape and the thickness of it will play a deciding part in the thermal protection it provides.
If a tape material that will withstand 1000F exposure is added to a hose, and the tape layer is 1/16" or 1/8" of an inch thick, it will provide a shorter cycle time than if it was 1/2", 1" or 2" thick. Although the tape material may be rated for 1000F, it will not keep the hose inside it cool unless the cycle time is considered and taken into account. Most non metallic rubber and synthetic hoses (and insulation on wires and cables) will have a temperature limit of well below 1000F.
Additional cooling or heating
In cases where the environment is very hot continuously (or cold), and the flow through the hose is low, then it may require additional cooling (or heating) mechanisms, such as a cooling (heating) liquid line in parallel to the hose (such as a water jacketed Electric Arc Furnace (EAF) cable), or a flow of forced cooling or heated air between the hose and the tape, or for freeze protection a heat trace heating tape.
In some cases the appropriate tape selection is a mixture of tapes: for example, an inner insulation tape and an outer heat reflecting tape. Some environments may require a tape with a coating on one side to provide a barrier to air flow as well as a barrier to contamination or flame exposure or weld splatter.
Choice of material - higher temperature rating does not mean it insulates better
And a final note on choosing thermal insulation / protection tapes. Take an example of a small wire or hose where protection is required as it passes through a hot area of a thermal process lets say running at 1200F. There are tapes available for temperature ratings of 1200F (fiberglass), 1382F (basalt), 1500F (vermiculite coated fiberglass), 1800F (silica), and 2190F (Ceramic), all with the same wall thickness. You might want to choose the 1800F silica or even 2190F ceramic tape as its has the highest temperature performance and you might think highest insulation value. In fact, all the tapes of the same wall thickness will have almost identical insulation values - so the 1200F fiberglass is your best and most economical choice without considering any other factors. The temperature rating of the material is not the only parameter to consider when choosing a material and a higher temperature rating does not mean a higher insulation value.
Free technical support - consult with us and avoid failure
We have many years of experience in these heat soak applications where hoses, wire and cables are exposed to continuous high environmental temperatures. Please contact us with your details so we can make the correct recommendation of materials and thickness. Details such as hose or wiring material, hose/pipe/wire/cable size, total length, type of medium (liquid or gas), flow rates, medium temperature, target temperatures, ambient temperature, hot environment temperature, hose/pipe/wire/cable length inside hot environment area, type of heat source, flame or molten metal exposure, availability of auxiliary liquid or air cooling source, and other parameters are all important considerations.
Please contact our techncial support team by phone or email to discuss your application. Pictures and drawings are always helpful.